CASE STUDY
Four Roses Bourbon
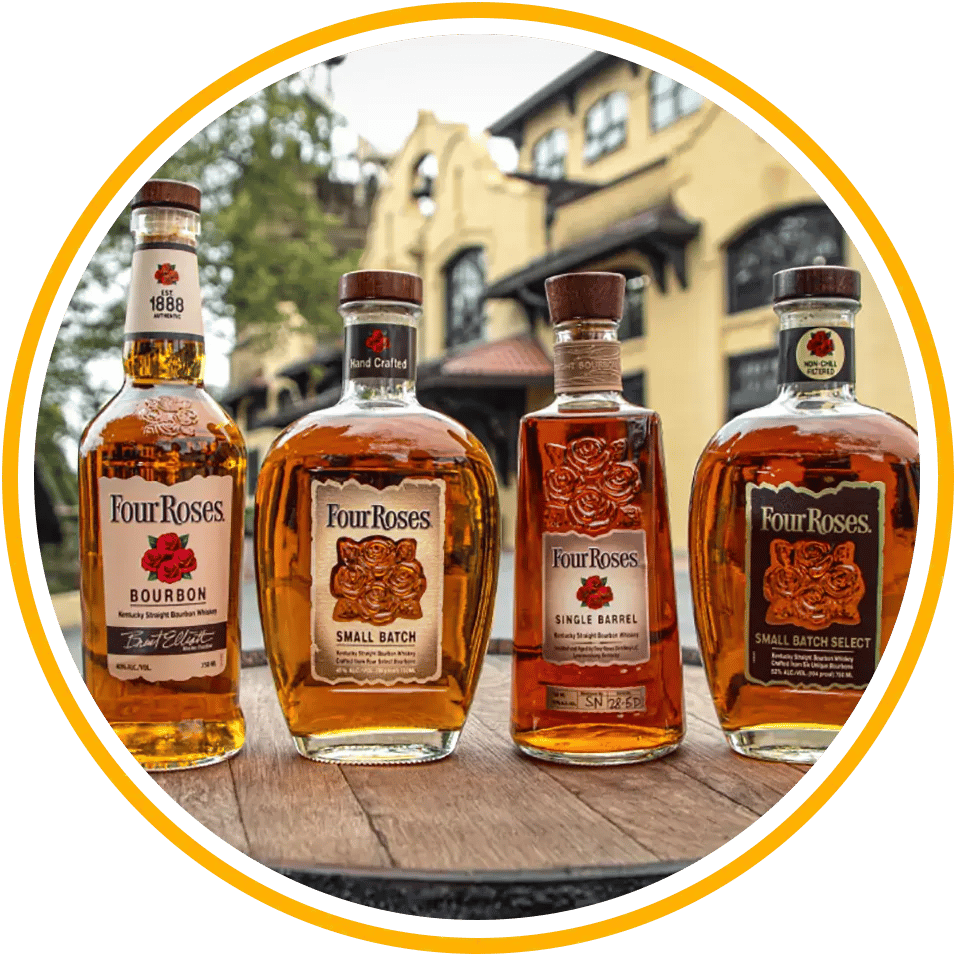
Automated MES & SCADA for Real-Time Production Tracking
The Protagonist

Four Roses Bourbon is a historic distillery for Kentucky straight bourbon whiskey. Founded in the 1800s, the company is known for its 10 classic recipes and highly sought-after limited-edition releases.
The distillery in Lawrenceburg, KY was built in 1910 with beautiful Spanish architecture. It is a tourist destination for bourbon lovers and the place where Four Roses' recipes are produced and mixed to create rich flavors. The bourbon is then mingled and packaged at their high-speed bottling facility in Coxs Creek, KY. The distillery produces around 4 million proof gallons a year and aims to double that capacity with a recently finished expansion.
The Story
In the Beginning...
Four Roses' production operations relied on manual processes consisting of extensive Excel sheets and handwritten lab notes. Data entry, calculations, and reporting took hours and there was no enterprise-wide way to track the path of grain from storage silos through warehousing.
The Plot Thickens
Four Roses needed a clear, automated way to track how much product was moving through distillation and bottling, and to see and understand all data throughout the process.
Vertech recommended a Track & Trace (MES) System with some SCADA elements and a separate OEE System to evaluate efficiency at their high-speed bottling line.
Vertech worked with Four Roses to build a process map to deeply understand Four Roses' existing process and map out all possible routes the grain could take during production.
Vertech worked with Four Roses to build a process map to deeply understand Four Roses' existing process and map out all possible routes the grain could take during production.
At the time, Four Roses Distillery had:
• 9 grain silos | • 48 fermenter |
• 3 meal bins | • 1 beer well tank |
• 2 cookers | • 1 high wine tank |
• 2 drop tubs | • 10 tank farm tanks |
• 6 yeast tubs |
Together, this equated to well over 710 total data entry points that needed to be captured and 622,080 possible grain pathways.
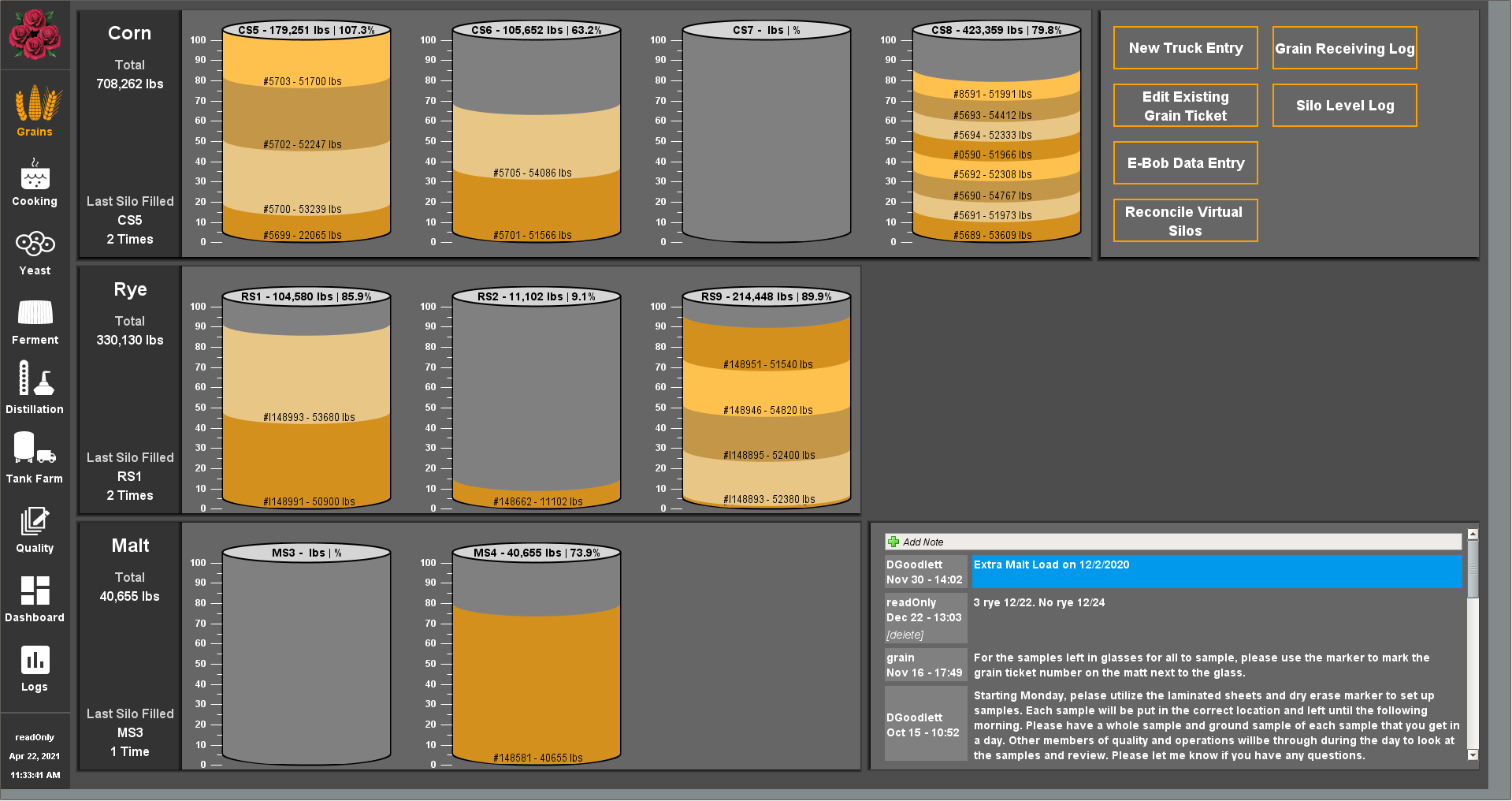
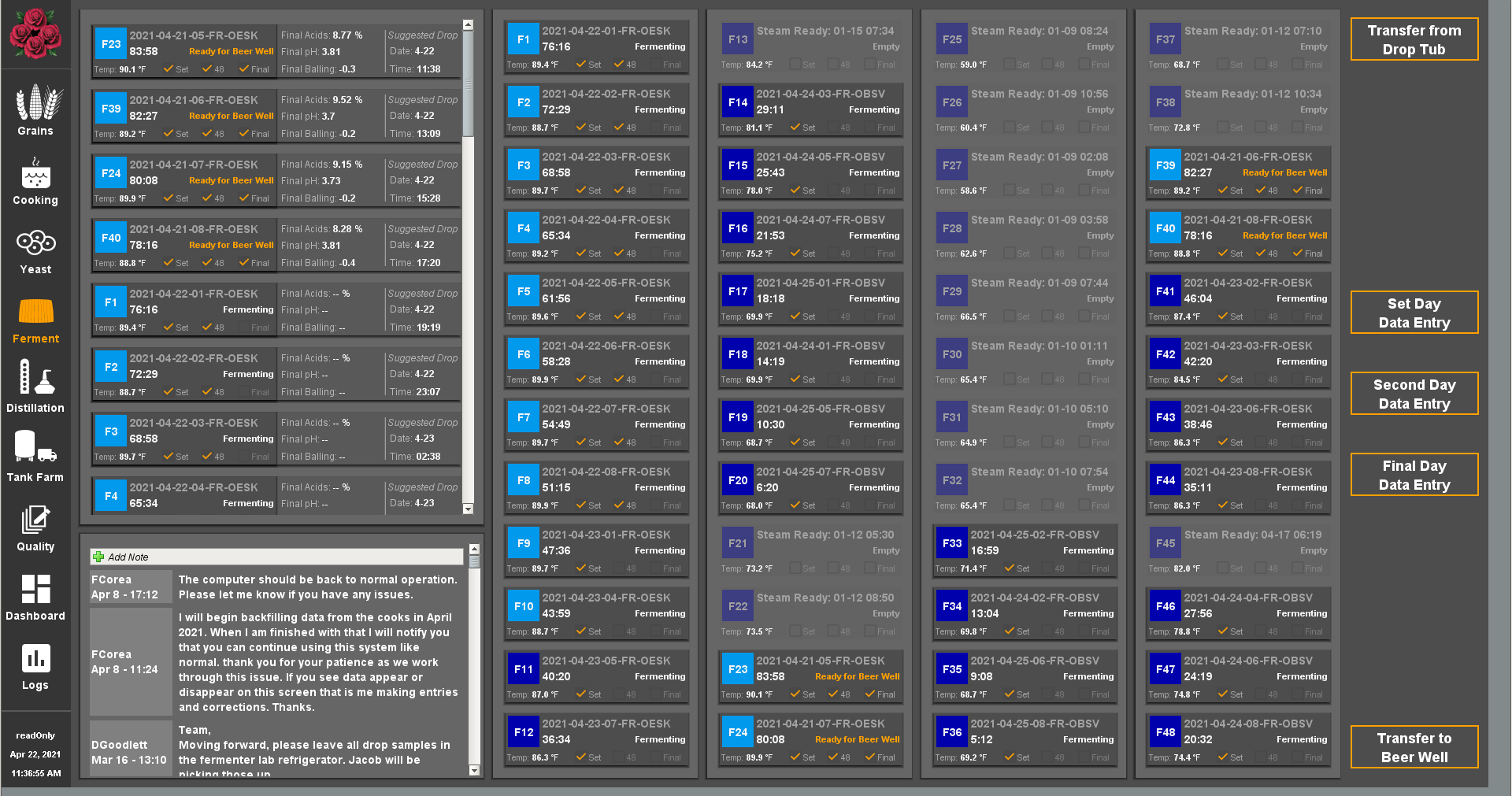
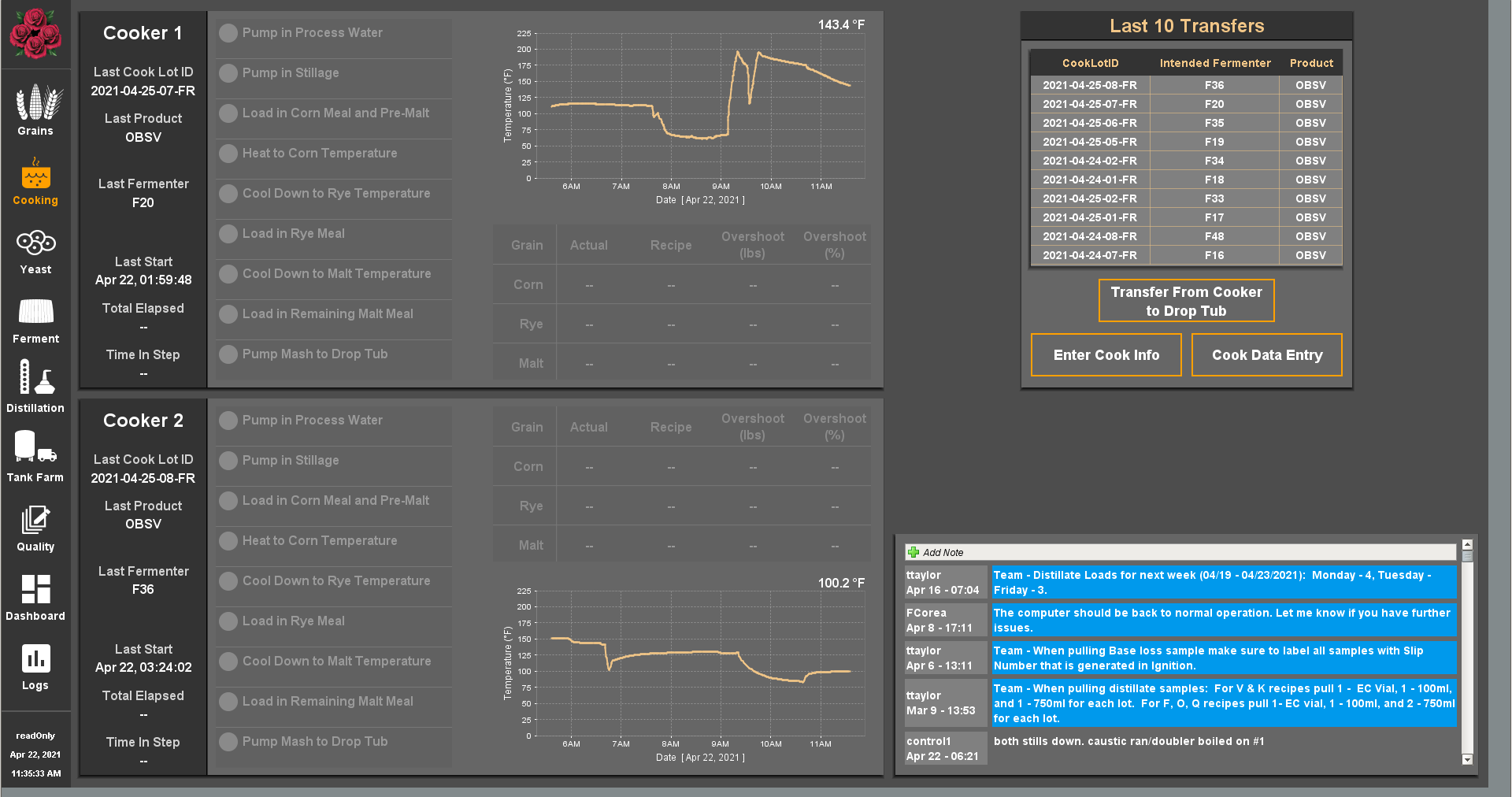
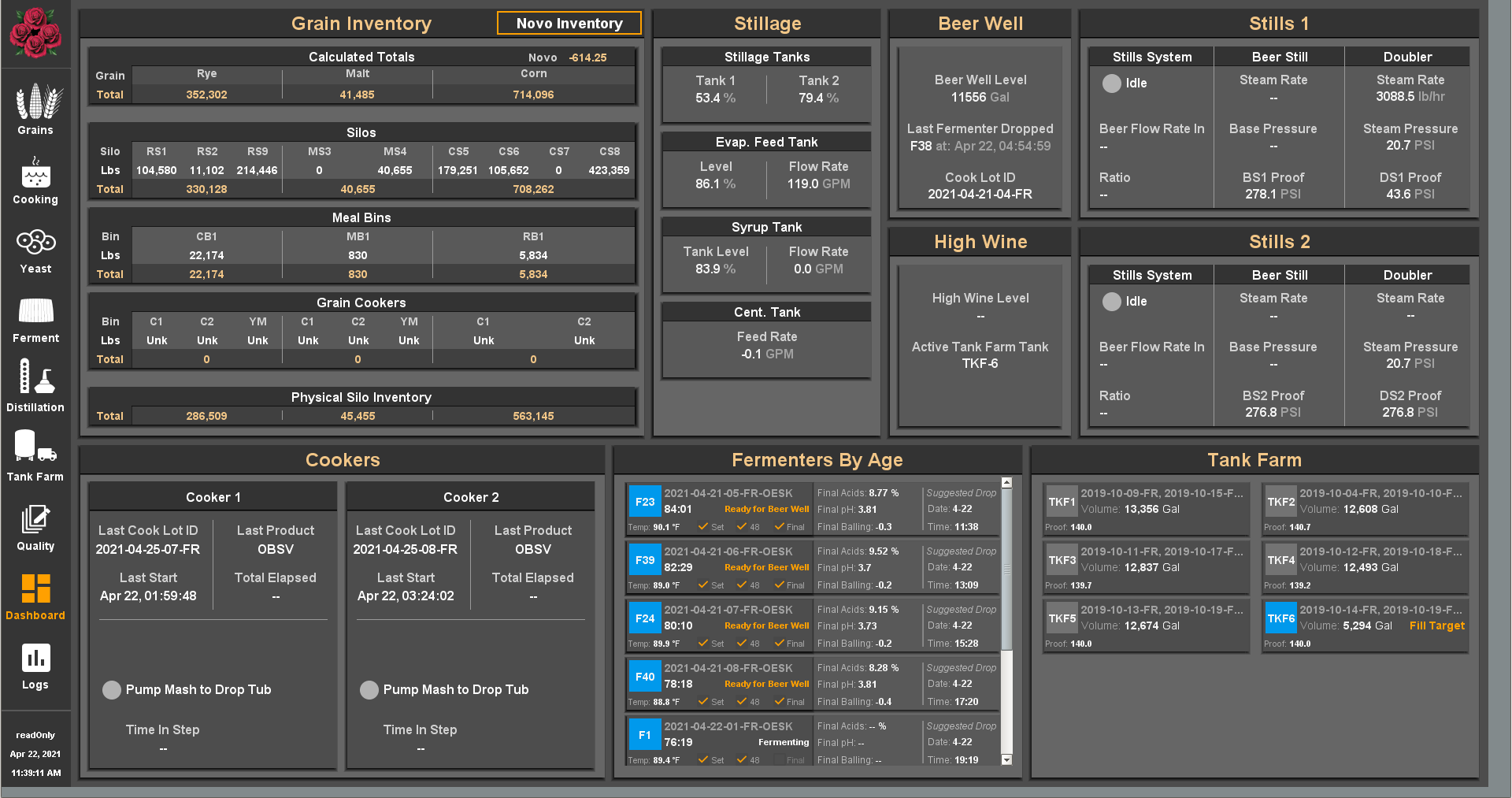
The System
Based on the process map, Vertech developed a framework and database design.
To better visualize the process and streamline all the data into one application, the team built a system with Ignition composed of multiple screens for each phase of distillation.
From grain truckload to shipping, the operators would have quick access to key information at every stage of the process.
Track & Trace
Since Four Roses uses a continuous batching process, Vertech decided to use the weigh scales under the bins to calculate the amount of grain inside and create batch records.
As the grain moves through each stage, new transactions are automatically created and associated with the batch record.
For easy operator access, Vertech leveraged Ignition’s extensive design capabilities to create 9 main screens for each of the following functions: Grains (storage), Cooking, Yeast, Fermenters, Distillation, Tank Farm, Quality, Dashboard (overview), and Logs.
The process stages of the facility are all linked through the Ignition connection to the MSSQL database. For example, as grain moves from the grain silos to the cookers, the tags associated with the process update various database tables; these tables provide a clear picture of how much of each grain moves into each cook batch and how much grain remains in the silos.
OEE (Efficiency Monitoring)
Vertech also designed an OEE system to monitor the high-speed bottling line, where the bourbon is blended and bottled.
The system has a process screen displaying the infeed count for the filler as well as various inspection points, including case weight, fill level, and label and cap inspection. It also monitors the rate of the labeler, the sealer, and the palletizer.
The OEE screen tracks overall equipment performance, including accurate production speed, line status, downtime (and reason code), and delays. It uses these inputs to calculate Four Roses' OEE score by production line, cell, product, shift, and timeframe. This data can be broken down further through the data analysis and history screens.
Technology Used
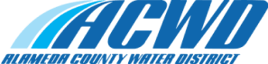
.png?width=117&height=80&name=arizona-tea-font%20(transparent%20background).png)
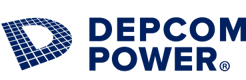
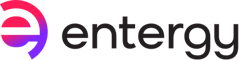
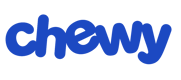
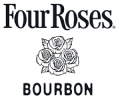


.webp?width=155&height=70&name=Rectangle%208%20(1).webp)
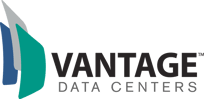
Application Features
Smart Alarming
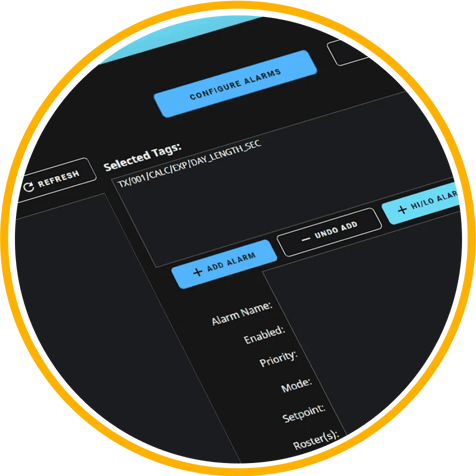
Nuisance Alarm Filtering.
We improved the alarming logic across the fleet to prioritize alarms and consolidate repeat alarms into one action.
Built-in Alarm Hierarchy and Dependencies.
This feature allows the client to add dependencies to alarms. When equipment upstream fails or shuts down, the alarms on downstream devices automatically shut off. This enables the client to identify and solve the root cause of the problem, rather than responding to hundreds of subsequent alarms.
Enterprise-Level Maps
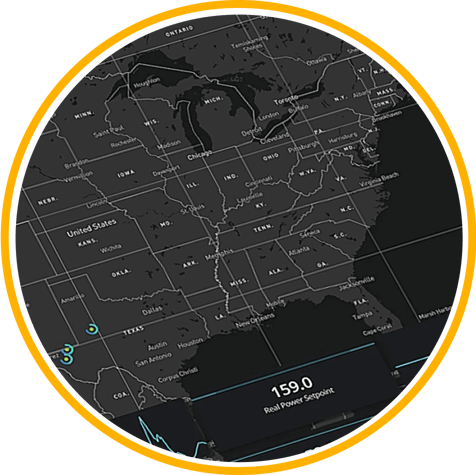
KPI’s
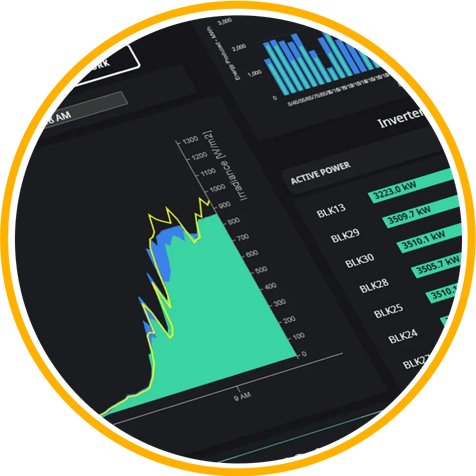
Power and Revenue
Our team collaborated with SB Energy to measure power and revenue using KPIs. By having the system display information from both business and operations in one application, decision-makers now have a clear understanding of what's happening across the entire portfolio.
Data Popups
Alongside the KPIs, trending popups allow operators and management to keep up with real-time data patterns and stay aware of site curtailments and revenue losses.
Weather Forecase Integration
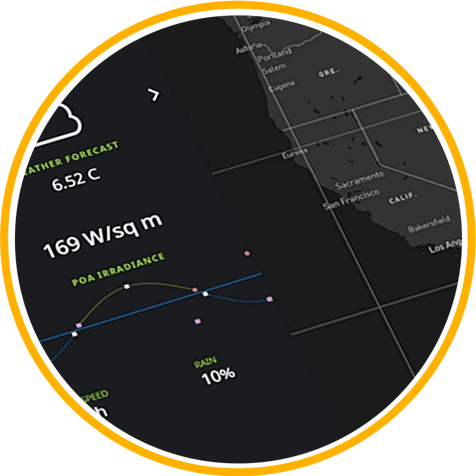
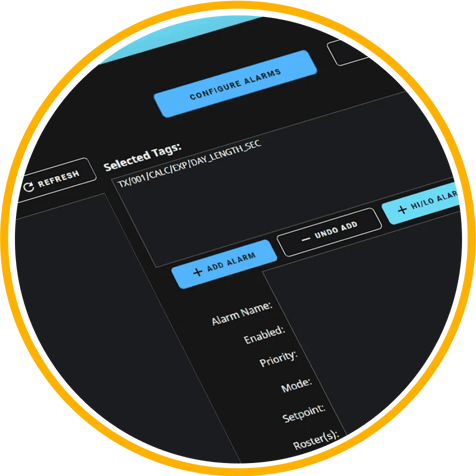
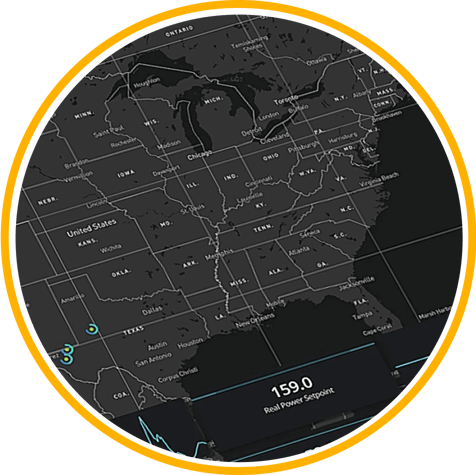
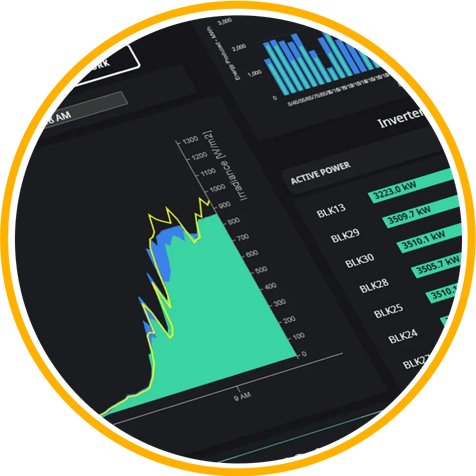
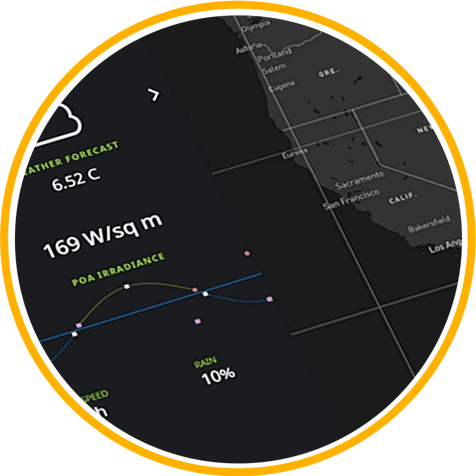
The Technology
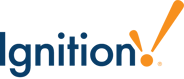



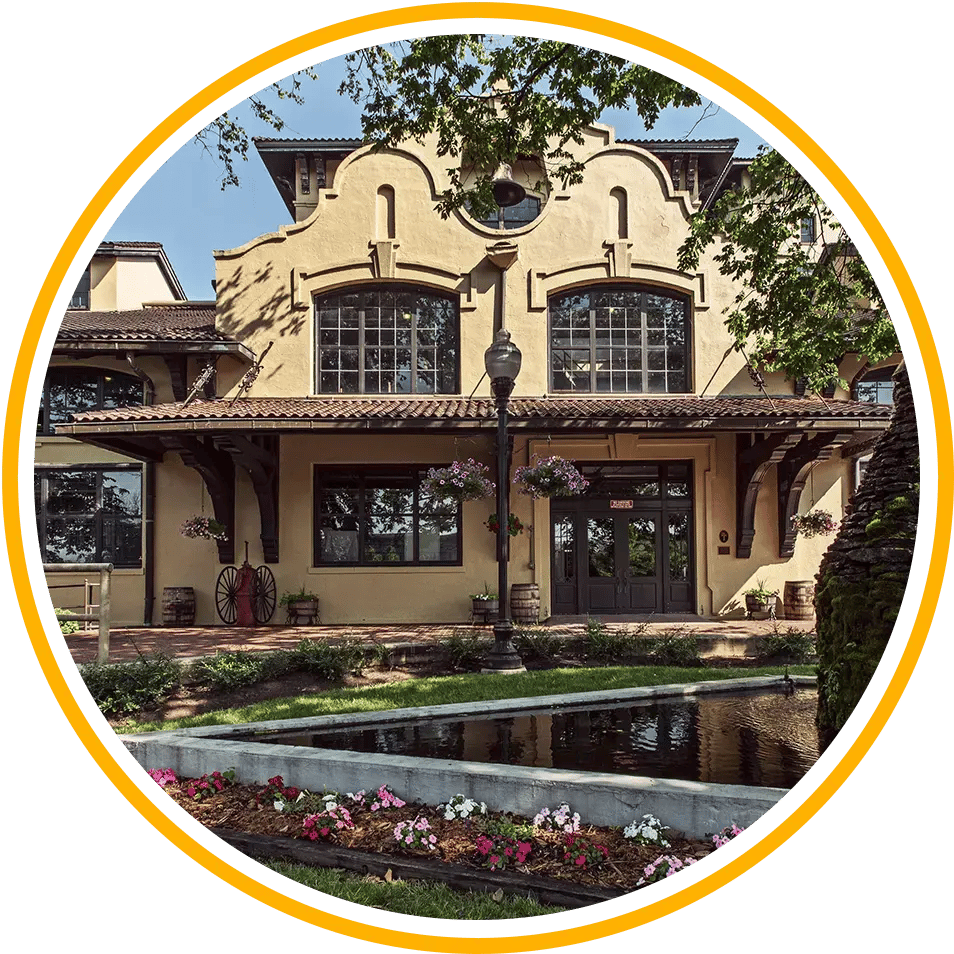
The Results
The system greatly improved Four Roses' ability to easily see their facility processes and keep track of all of the data needed to effectively run the plant.
By giving Four Roses a view into real-time production, efficiency, line reliability, as well as top problem areas, managers can gauge whether process changes or continuous improvement projects are effective.
Drop us a line
If you'd like to learn more about how we can improve your operations, get in touch!
We love a good challenge and we're ready to help.
.png?width=750&height=679&name=247Support%201(1).png)