CASE STUDY
Anchor Brewing
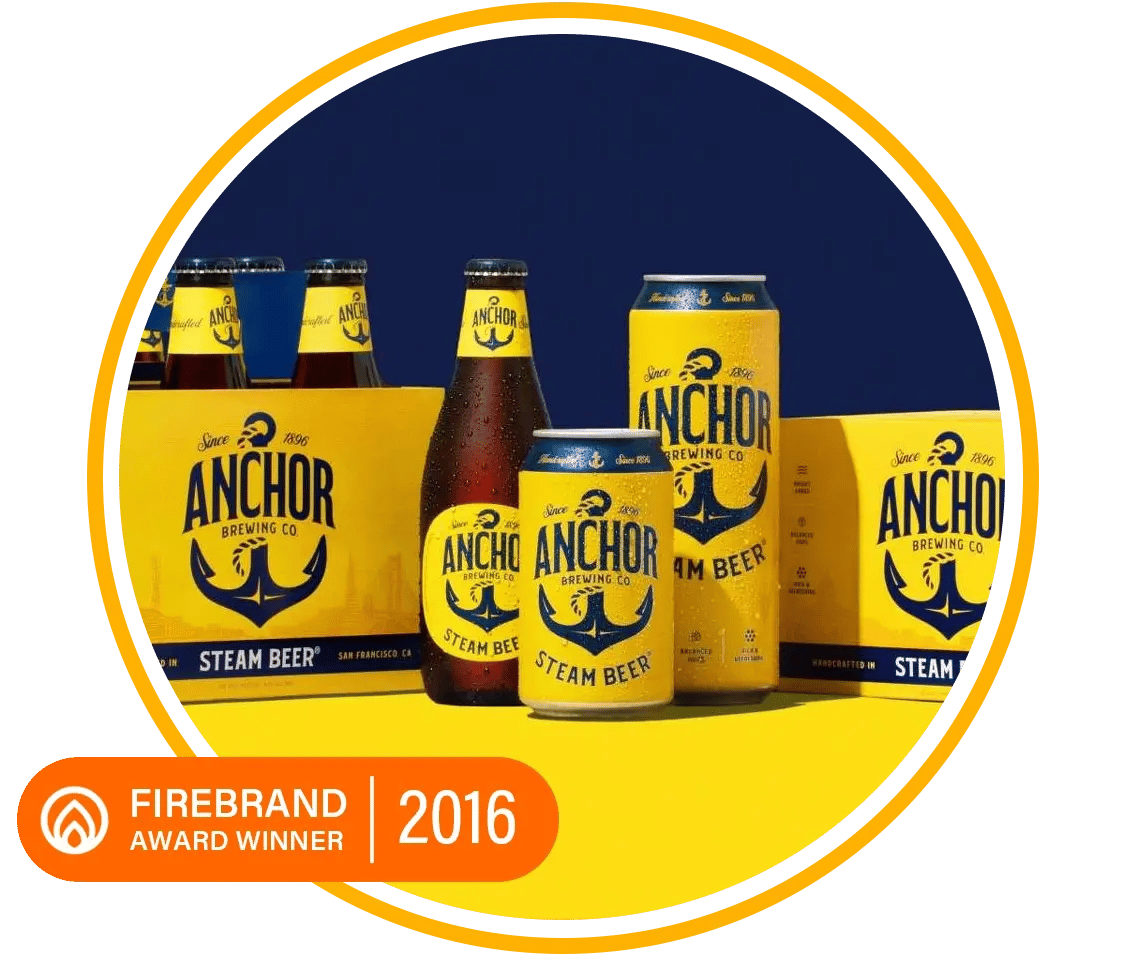
Brewery White Box Ignition MES Solution Enhances Production Visibility and Efficiency in One Day
The Protagonist
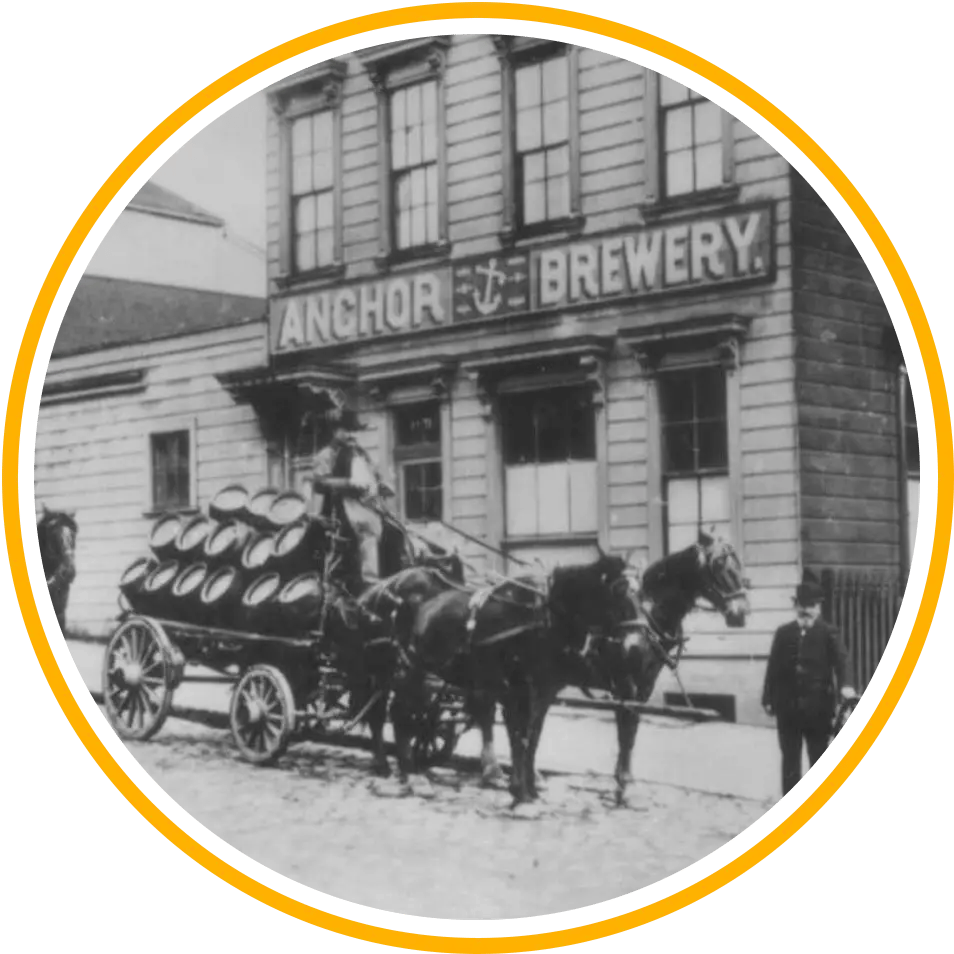
Anchor Brewing one of America's oldest craft breweries. Founded in 1896, it became famous for its Steam Beer—a uniquely Californian style brewed with lager yeast at warmer ale temperatures. Over the decades, Anchor set the stage for the craft beer movement, focusing on tradition, quality, and innovation. Its legacy of bold, flavorful beers and deep ties to San Francisco's brewing history make it a beloved name among beer lovers.
The Story
In the Beginning...
Production facilities like Anchor Brewing run at a lightning fast pace and every minute of downtime and each incidence of waste translates to a big cost. Vertech wanted to automate the gathering of production rates, waste, and downtime on a running line without interrupting production in any way on dozens of customer lines, network configurations, PLCs, meters, and brands. Vertech needed to find a way to create a compact but powerful analysis machine that only required a single power outlet and a single network connection.
White Box Requirements:
- It must install in one day without any downtime on the line.
- It must be a “Swiss army knife” type of product that can connect to any PLC, power source, line configuration, and any sensors.
- Everyone in the facility must have access to the data.
The Plot Thickens
To fit such a dynamic and varied set of hardware, Vertech utilized Inductive Automation’s Ignition software, which seamlessly connected to the client’s existing control systems, including the PLCs, photo eyes, and flow meters. By supplementing an on-board Siemens PLC, including Vertech’s PLC code for dozens of instruments and scaling routines, we were able create an instant drop-in control system that sits in parallel to existing infrastructure.
The Happy Ending
The resulting system was installed in days without interrupting production, and takes less than five minutes of operator interaction per shift. It can record, analyze, and display production data with a simple, intuitive operator interface, and provides high-level cost analysis and report generation for supervisors, accessible on any device.
From day one, the White Box constantly gathers production data that is instantly available to view and explore. The simple configuration includes the actual products, SKUs, case configurations, line rates, financial data and specific downtime reason codes from the brewery. Operators are able to see planned production, progress, performance, downtime and expected delays. The operator screens use HMI optimization tactics to quickly communicate the most important information while not distracting people from operating the line. Supervisors, plant managers, and other executives are able to see real-time performance, run progress and top downtime reason codes.
Additionally, there are historical screens that show all production runs, charts of the best and worst runs from the perspective of OEE, and a production analysis screen. The analysis is available for any line over any time period and for a single product or all products. The screen is an easy-to-understand analysis of the labor losses, yield losses, the loss distribution by product and the improvement.
Anchor Brewing Company found enough low-hanging opportunities to have a complete ROI in 12 months. Prior to using the White Box, Anchor was certain that its line ran at 415 bpm through manual OEE tracking, and was shocked to find that on average it ran at 322 bpm and never exceeded 365 bpm. Here's to accurate, accessible, real-time data!
Watch the Case Study
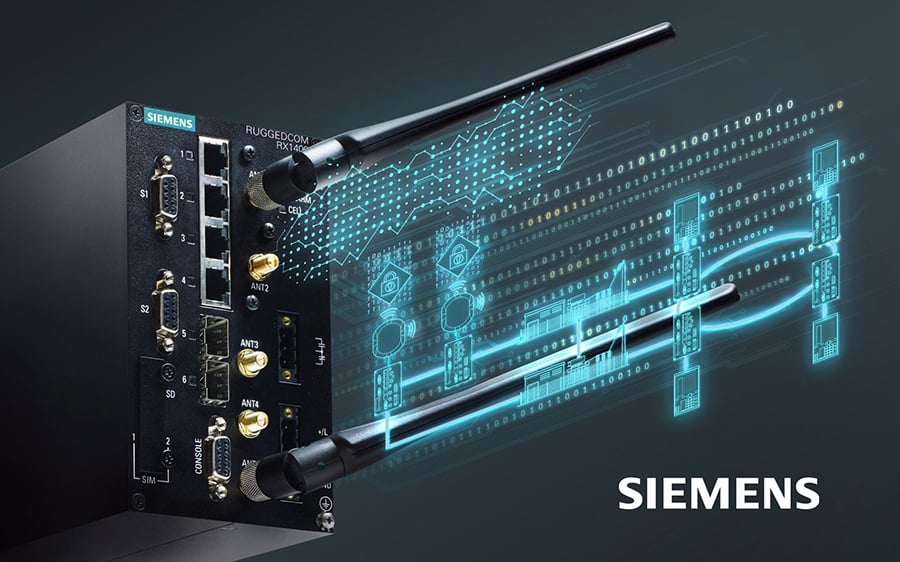
Technology Used
- IA Ignition HMI SCADA
- IA Ignition MES
- Siemens 1215C PLC
- Siemens W774 WAP Radio
- Siemens Switches
- Siemens Industrial Computers
- Cisco Wireless VPN Firewall
.jpg?width=2000&name=Frame%20299(7).jpg)
(1).jpg?width=2000&name=Frame%20299(1)(1).jpg)
(1).jpg?width=2000&name=Frame%20299(2)(1).jpg)
(1).jpg?width=2000&name=Frame%20299(3)(1).jpg)
(1).jpg?width=2000&name=Frame%20299(4)(1).jpg)
(1).jpg?width=2000&name=Frame%20299(6)(1).jpg)
(1).jpg?width=2000&name=Frame%20299(5)(1).jpg)
Application Features
Smart Alarming
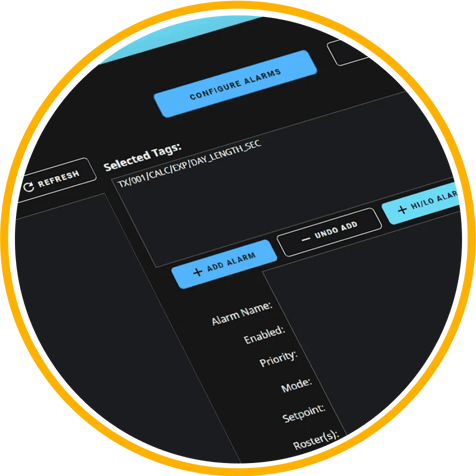
Nuisance Alarm Filtering.
We improved the alarming logic across the fleet to prioritize alarms and consolidate repeat alarms into one action.
Built-in Alarm Hierarchy and Dependencies.
This feature allows the client to add dependencies to alarms. When equipment upstream fails or shuts down, the alarms on downstream devices automatically shut off. This enables the client to identify and solve the root cause of the problem, rather than responding to hundreds of subsequent alarms.
Enterprise-Level Maps
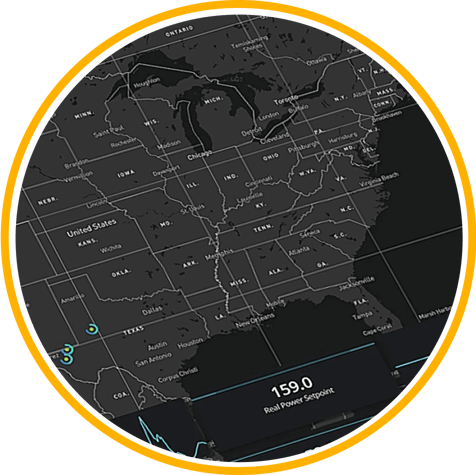
KPI’s
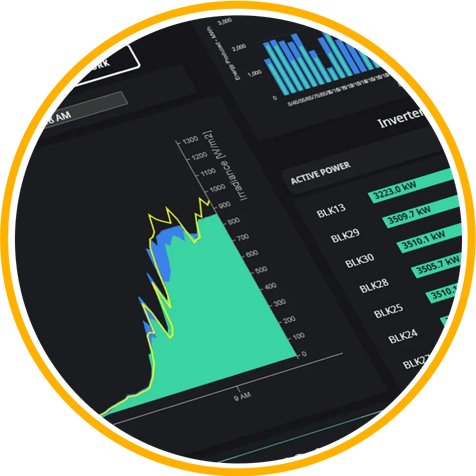
Power and Revenue
Our team collaborated with SB Energy to measure power and revenue using KPIs. By having the system display information from both business and operations in one application, decision-makers now have a clear understanding of what's happening across the entire portfolio.
Data Popups
Alongside the KPIs, trending popups allow operators and management to keep up with real-time data patterns and stay aware of site curtailments and revenue losses.
Weather Forecase Integration
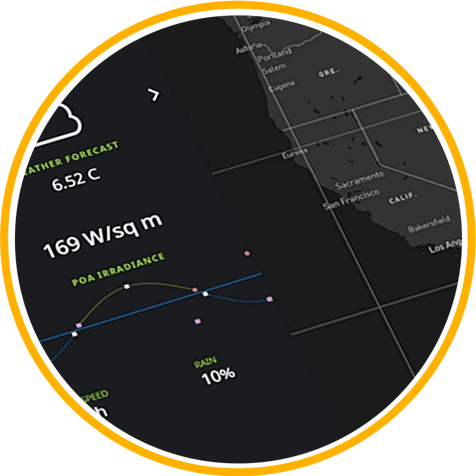
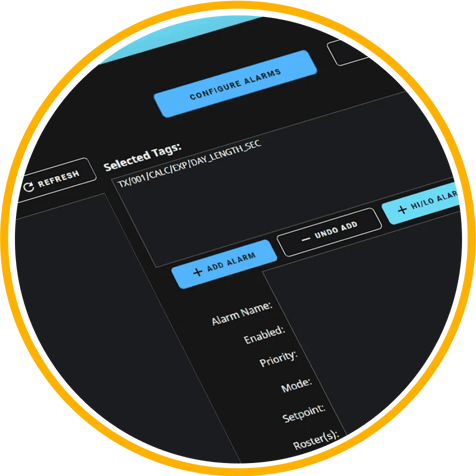
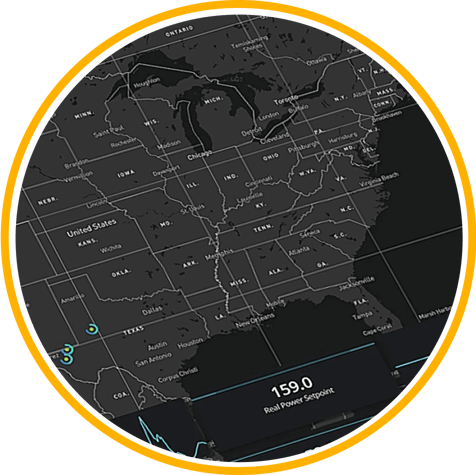
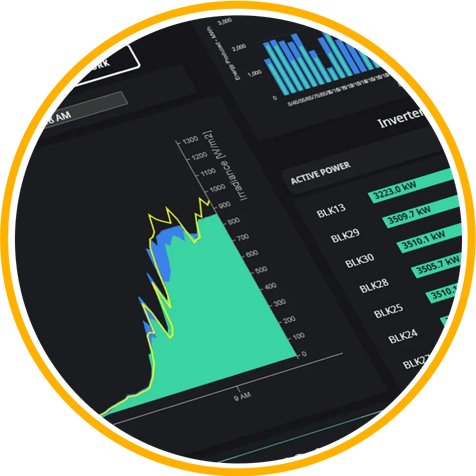
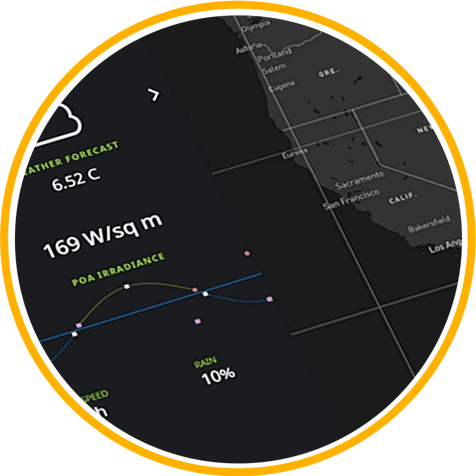
Drop us a line
If you'd like to learn more about how we can improve your operations, get in touch!
We love a good challenge and we're ready to help.
.png?width=750&height=679&name=247Support%201(1).png)