CASE STUDY
Amy's Kitchen
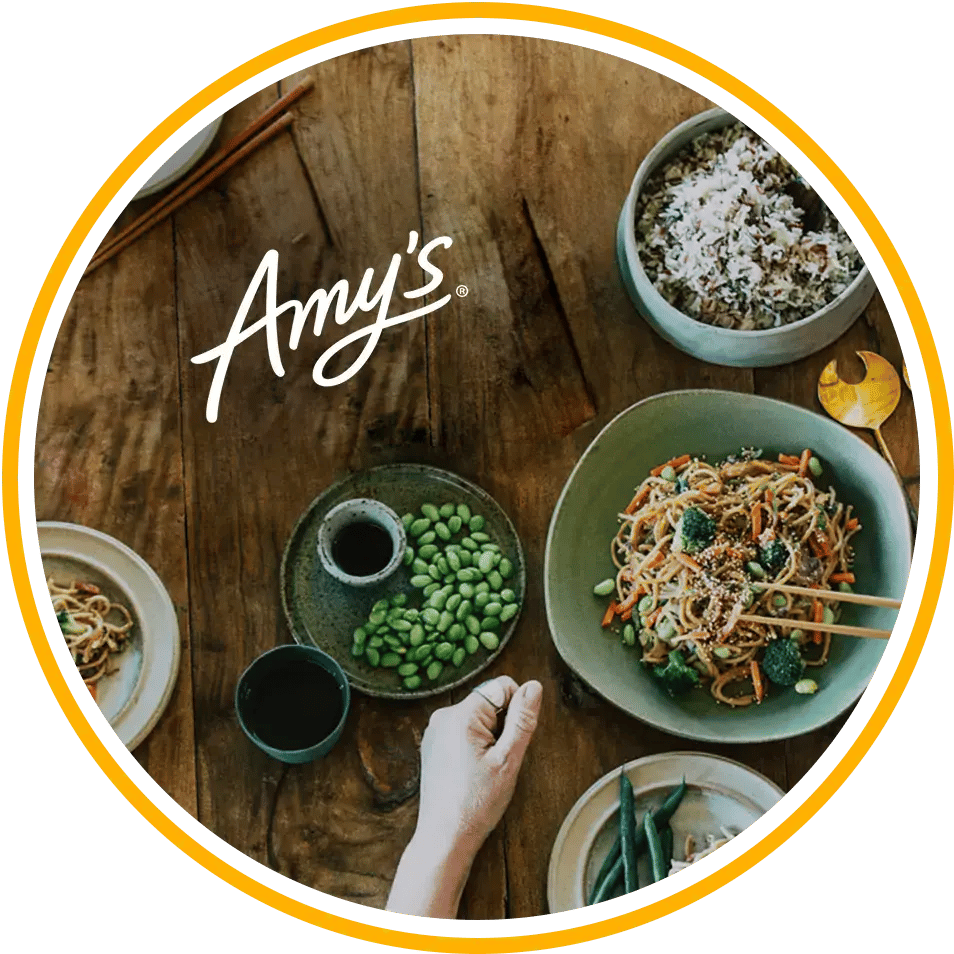
OEE Efficiency Tracking
Enterprise SCADA Streamlines Processes for Renewable Energy
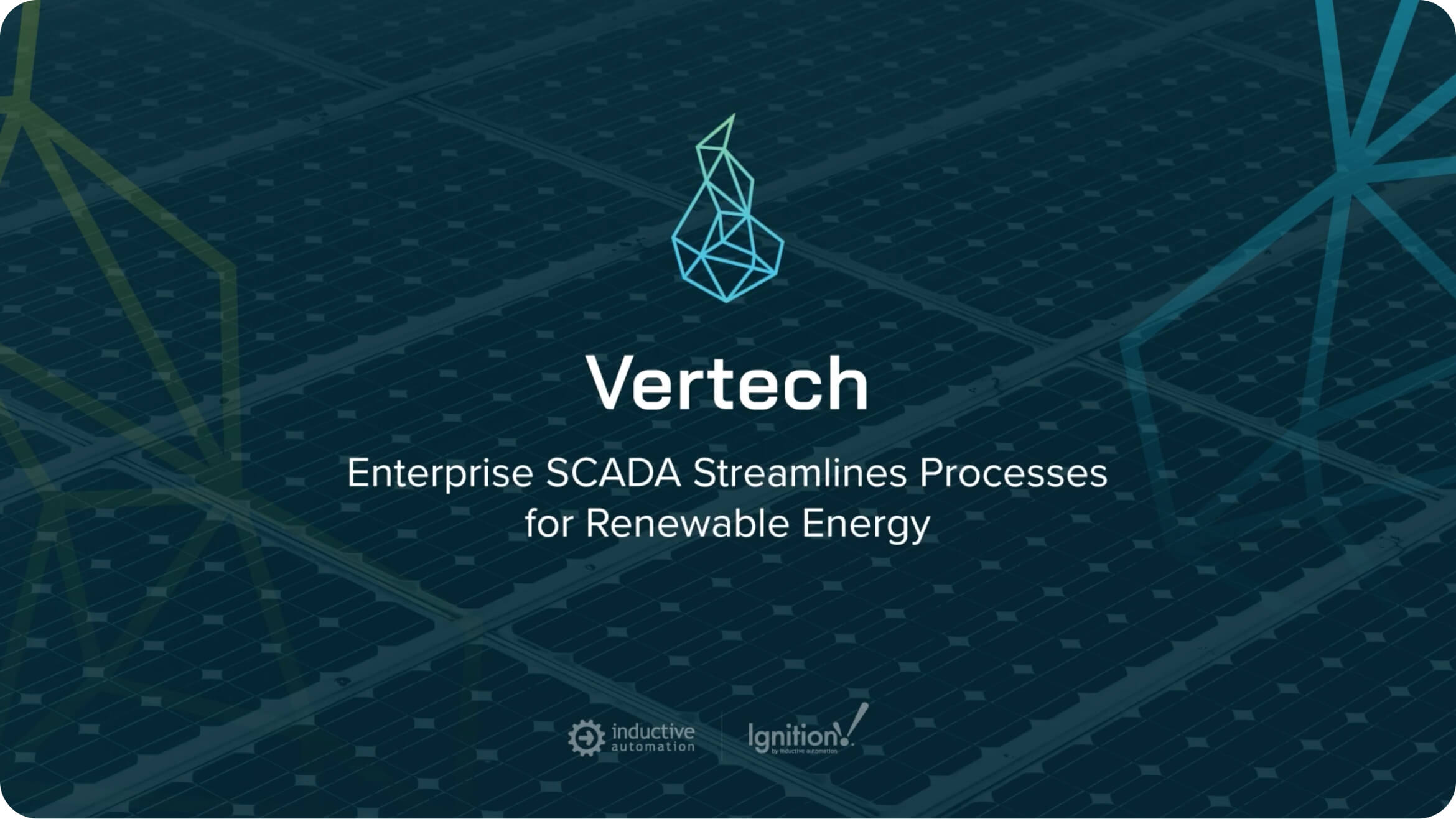
The Protagonist
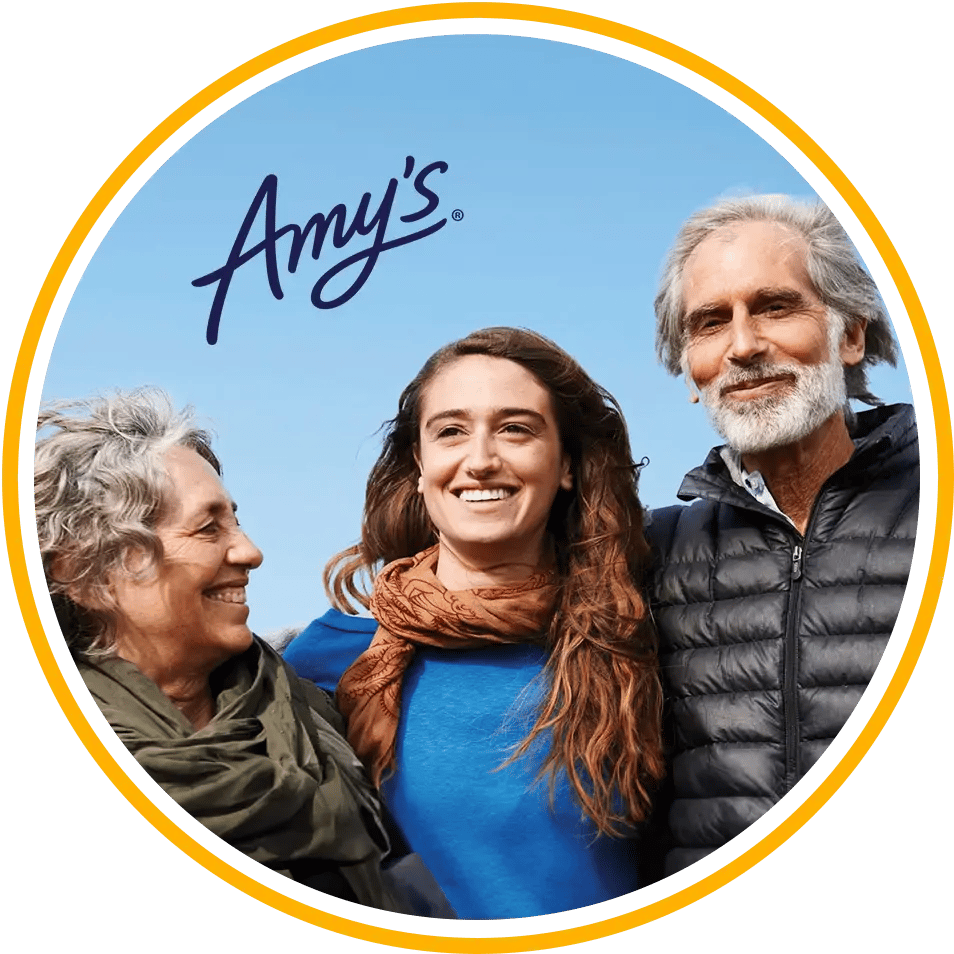
Amy's Kitchen is a family-owned company that manufactures organic and non-GMO convenience and frozen foods. Amy’s also offers a drive-thru with delicious healthy and vegan choices.
Founded in 1987, Amy’s Kitchen manufactures specialty convenience and frozen foods such as canned goods, pizza, burritos, veggie burgers and frozen entrees. Three of their sites are in Medford, OR, North Point, CA and Pocatello, ID.
The Story
In the Beginning...
Amy’s Kitchen requested an OEE system upgrade across three of their production sites to automatically track and display production efficiency and equipment downtime.
Instead of manually compiling data from various sources in excel, Amy’s Kitchen wanted a comprehensive solution that would tie into their ERP system and allow for easy display and analysis of all plant data.
The Plot Thickens
Two of the plants were using Redzone software, which has a high yearly subscription cost. As an off-the-shelf OEE package, Redzone also required them to build their process around the software, without a lot of flexibility. The third plant had no existing software in place.
One of the main challenges was determining how to keep track of batch production in real-time. Batches could be broken up into multiple production lines, with multiple starts and stops in production. The operator screens also had to work regardless of whether a line had automatic sensors or manual input.
Amy's Kitchen wanted a solution that would work well in their current set-up, but also allow the flexibility to continue to grow and change their processes without having to work around their software.
The System
Vertech replaced Redzone with industry-leading Ignition and Sepasoft software, eliminating the yearly subscription cost and allowing the engineers to customize the design for each plant.
There were 3 main design components for each site:
• Operator screens
• Manager screens
• Dashboard view
These worked together to quickly provide information to all levels of personnel at a glance.
For the operator screens, Vertech provided the ability to schedule automatic batch startup, adjust production rate depending on personnel, manually start and stop production, set downtime reason codes, and view the status of the entire plant.
The management screens were designed to allow managers to view real-time production, downtime history, production history, perform data analysis and create reports.
The dashboard view was developed to display production highlights at a glance on large overhead monitors. A simplified line status screen would show important information like whether a batch started on time, estimated completion time, production rate, and other real-time alerts.
Additional Features
Analysis Selector Tool
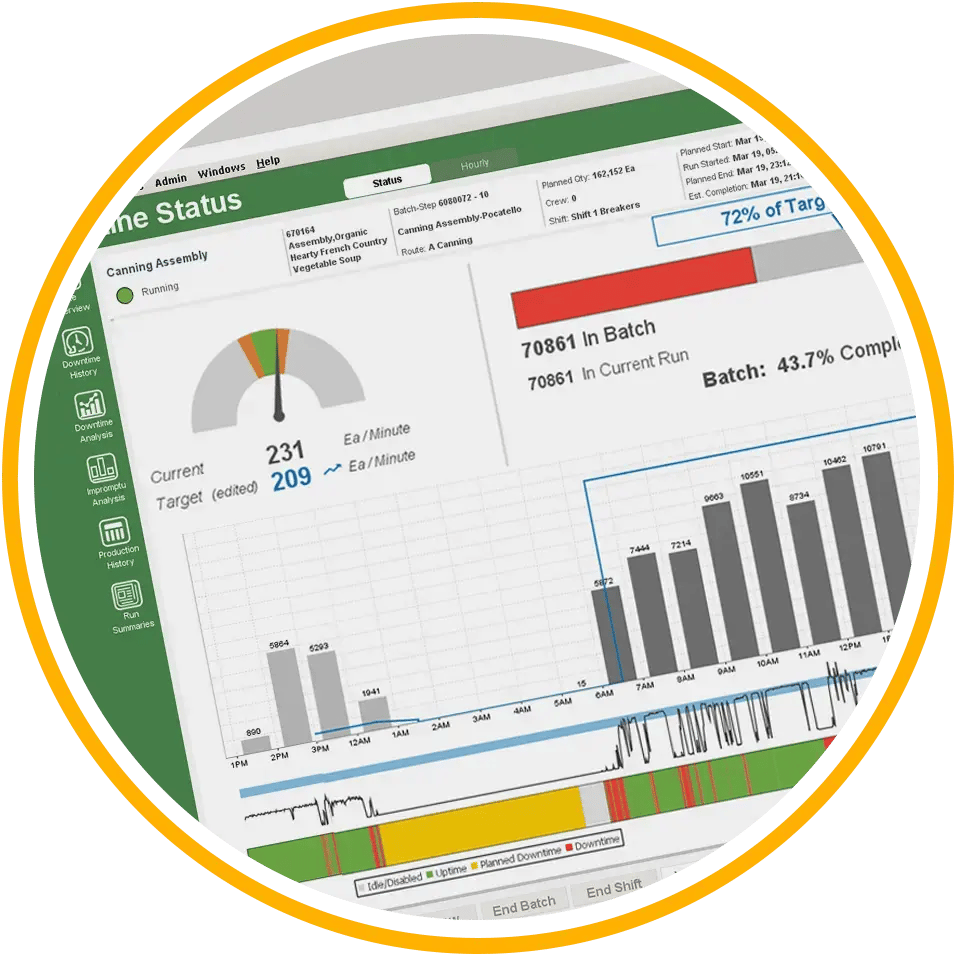
An analysis selector tool through Sepasoft, which allows the user to filter data points like outfeed count, lines in operation, and equipment status and quickly build out custom reports in table or graph formats.
Downtime Table Analysis
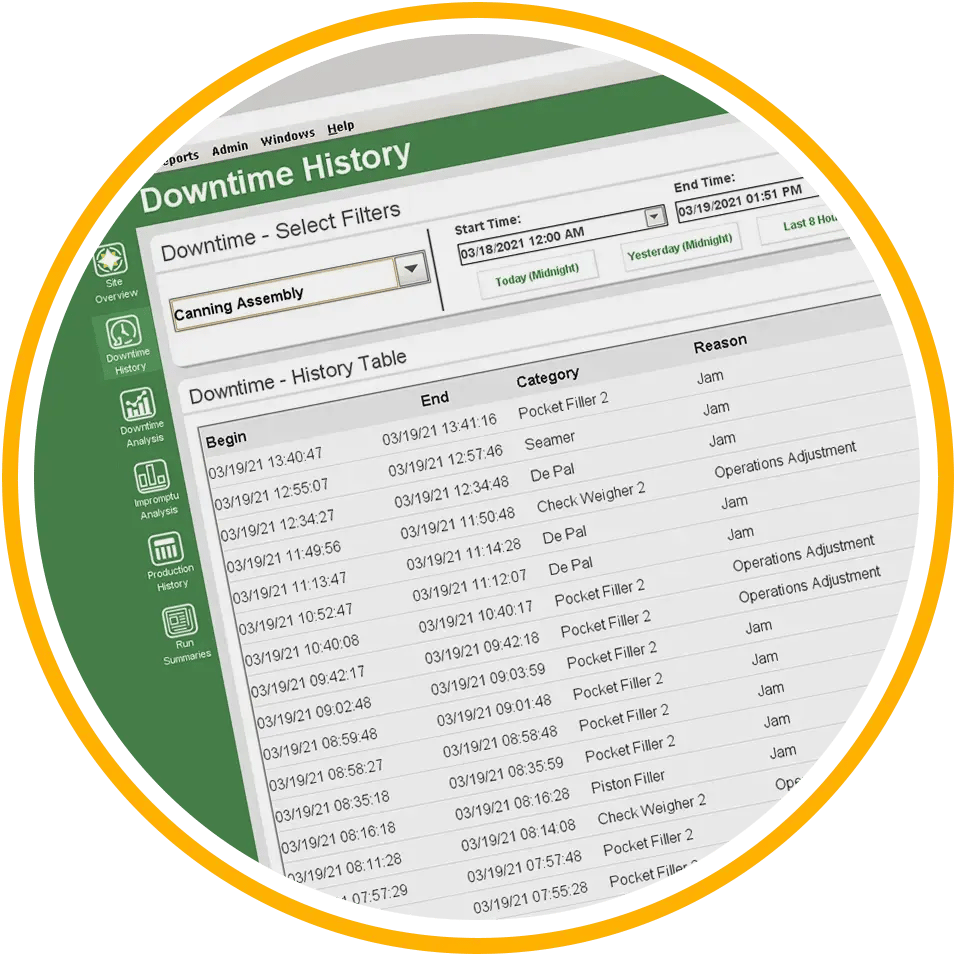
Downtime events can be filtered by line, shift, product, or area to run analysis on what the causes were. Events can be grouped and assigned to a reason for failure. Each event also contains a note field where more information can be added. This allows downtime reporting to be very specific and accurate.
Manual Data import
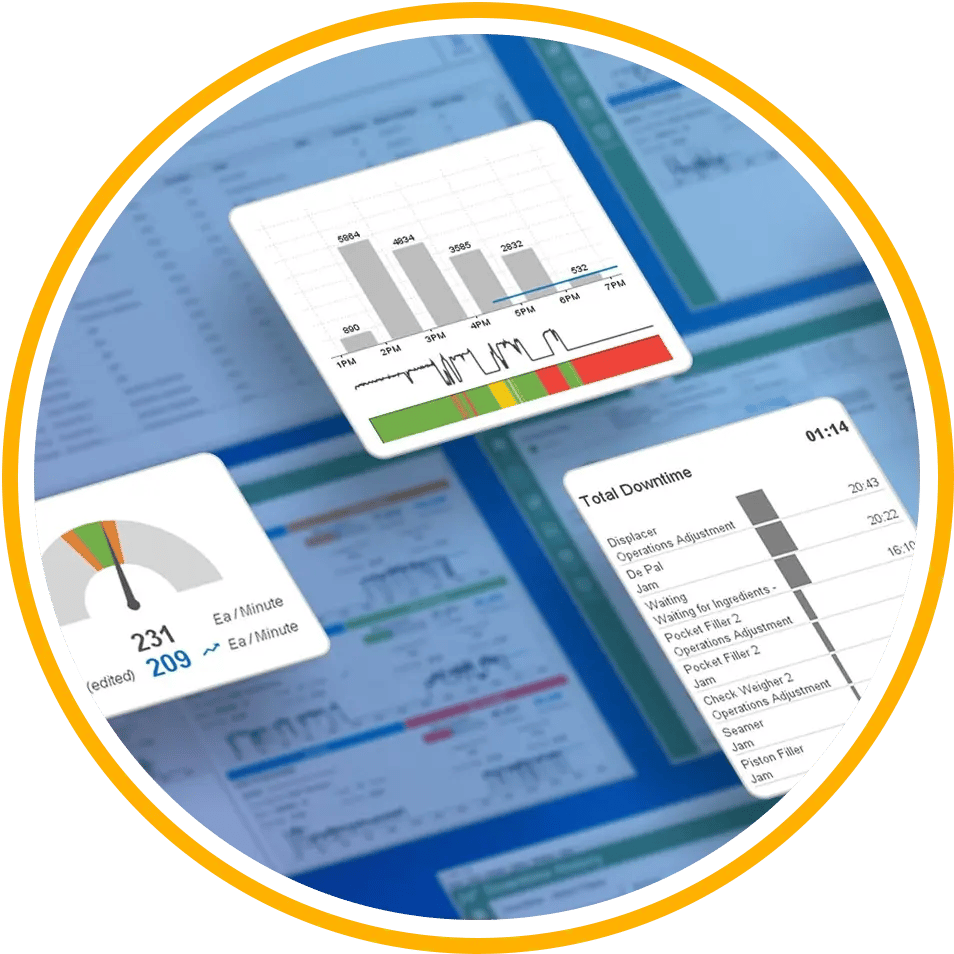
Additional Features
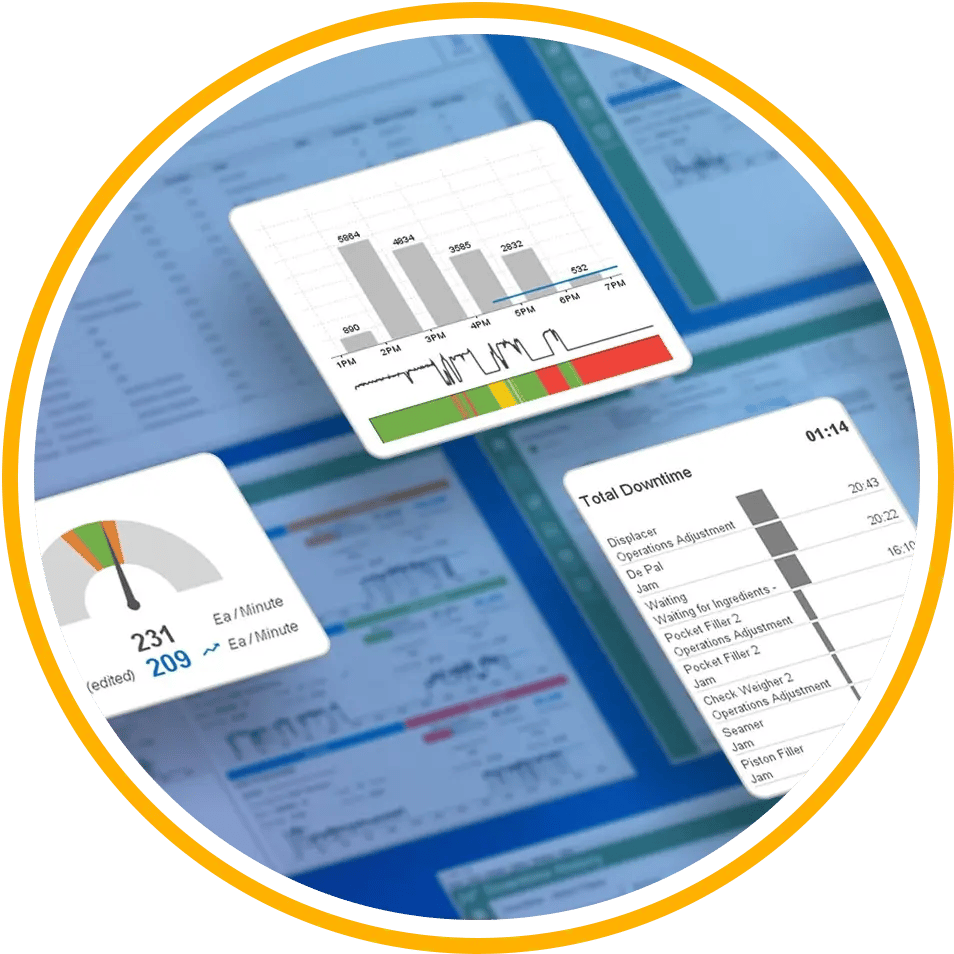
Production view toggles quickly switch between batch, shift, and day time frames.
A shift end feature, which allows for complete production control at the close of a shift. If a work order needs to be kept open through a shift change, the batch is automatically paused, all shift information is recorded, and the batch restarts with the new shift information.
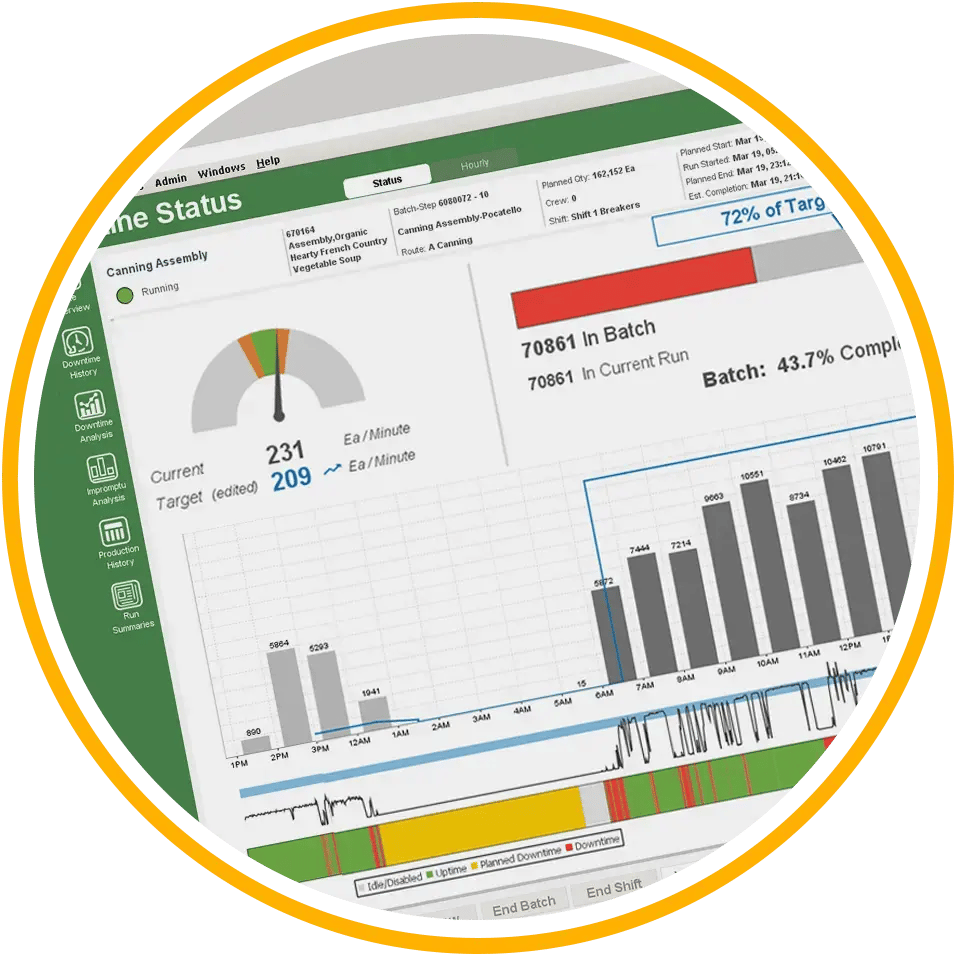
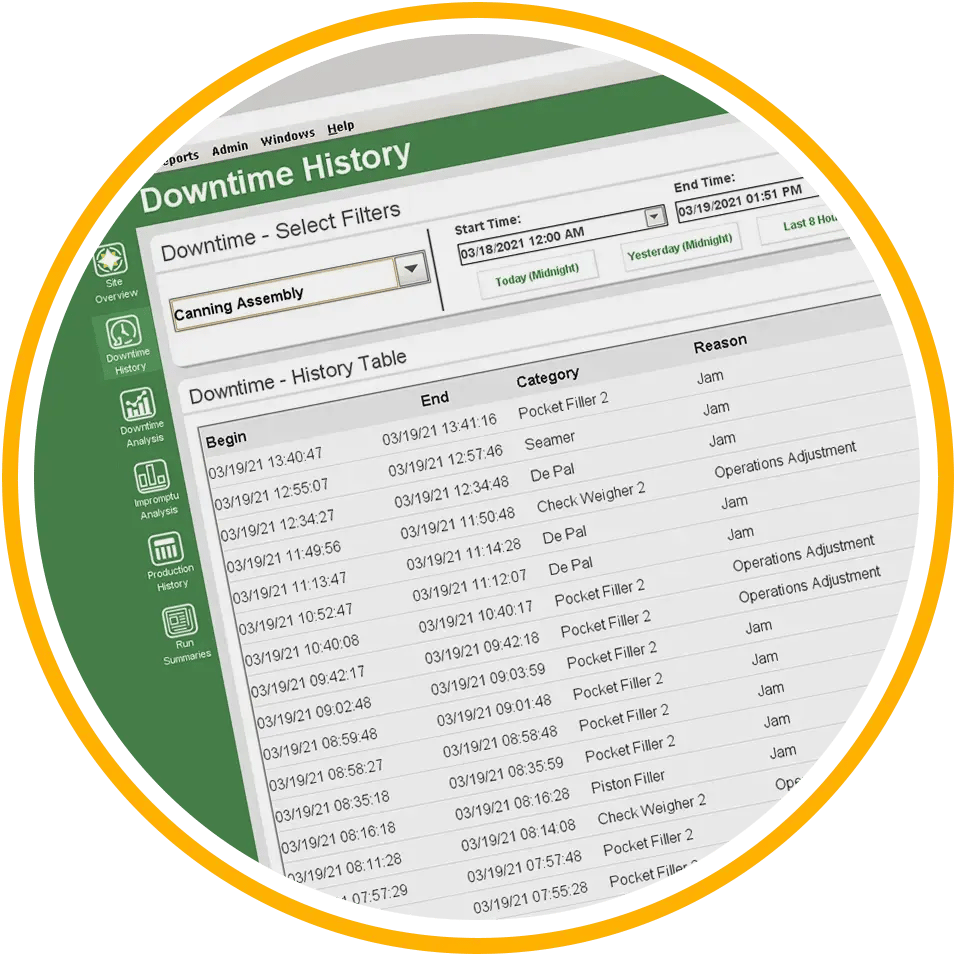
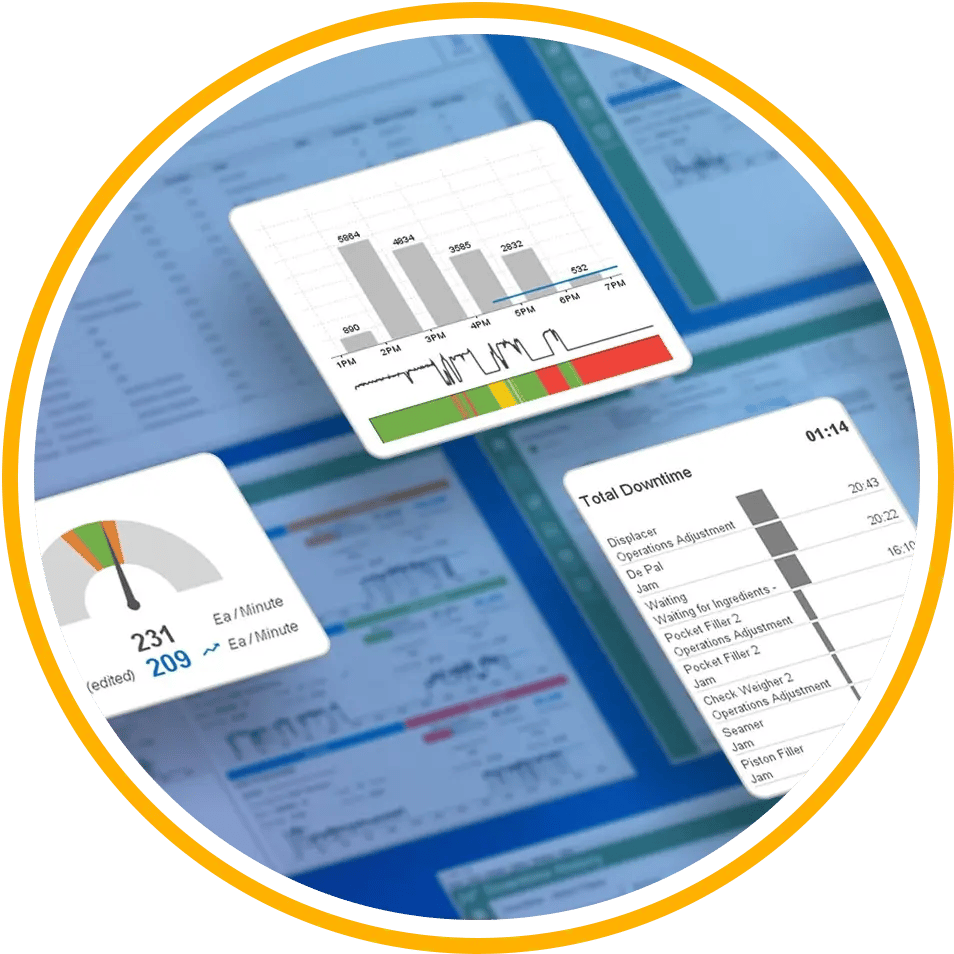
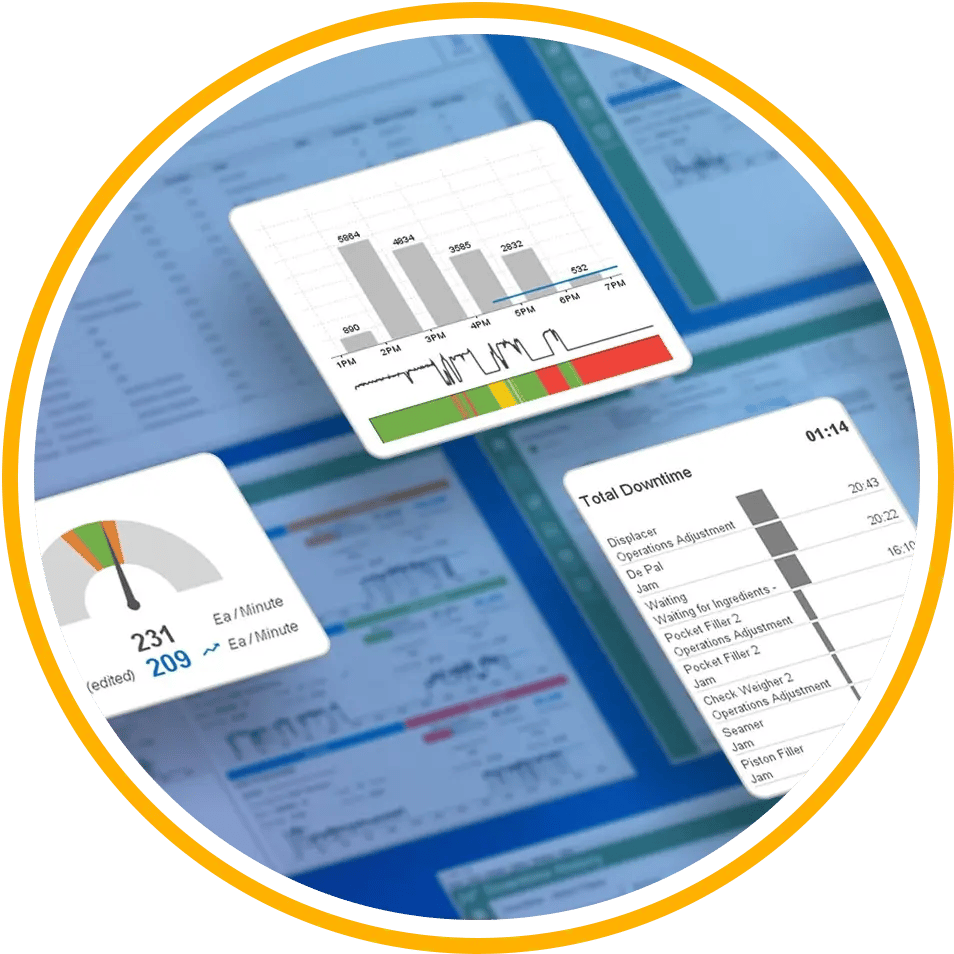
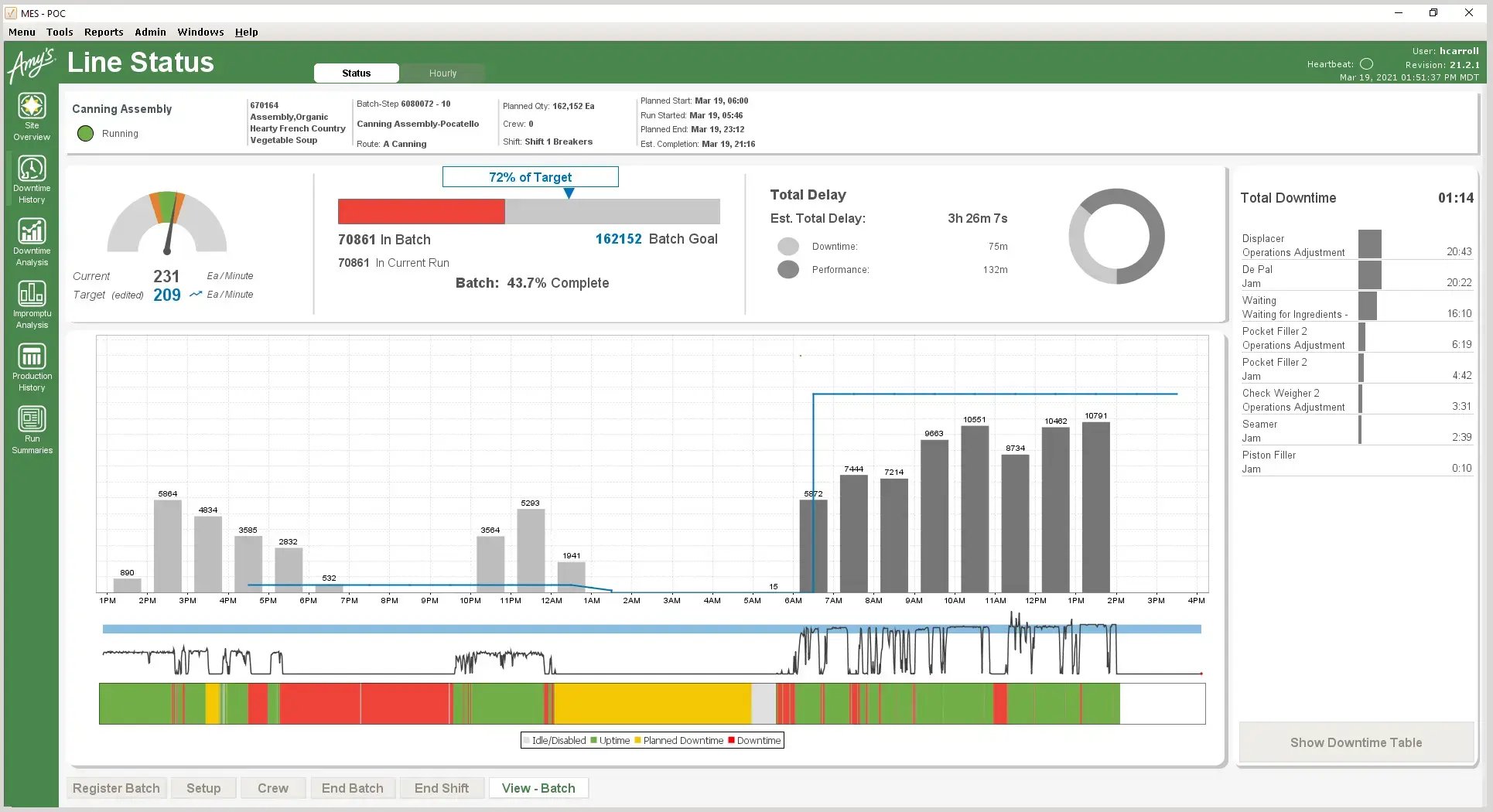
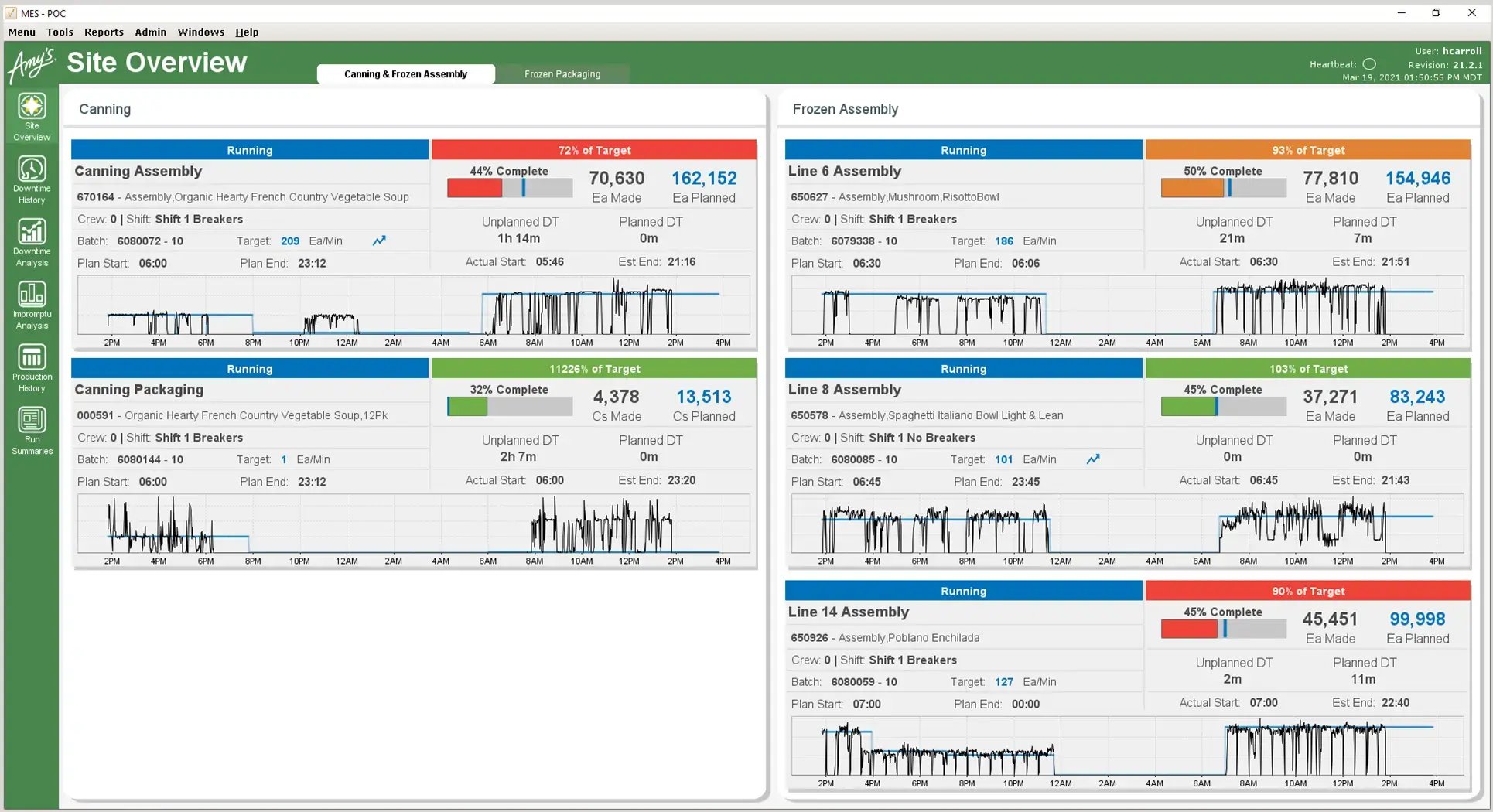

The Technology
Inductive Automation Ignition 7.9
Sepasoft MES Platform 2.0
Sepasoft 2.0 OEE Module
Microsoft SQL Server
Allen-Bradley ControlLogix
Allen-Bradley MicroLogix
Allen-Bradley CompactLogix
The Results
Vertech successfully designed and implemented the operator, manager, and dashboard screens, enabling real-time, comprehensive data collection and reporting on plant OEE.
Amy’s Kitchen has plans to expand the new OEE solution to other areas of their production as well as add more MES features down the road.
With real-time run data, it is now easier than ever to see if a line is delayed or is running too slowly to hit its target. Managers can also look at historical data and minimize downtime by suggesting changes in batch scheduling and execution. They can also easily create data reports that quickly identify issues with processes or equipment that need to be addressed.
Operators can make immediate adjustments to their line and report downtime issues as well as view all plant activity. With automatic batch-starting and SKU creation, the new system now reduces the prep time needed for configuration and maintenance.
Vertech’s flexible design using Ignition software allowed them to take greater ownership of their process and continue to plan for future improvements to production.
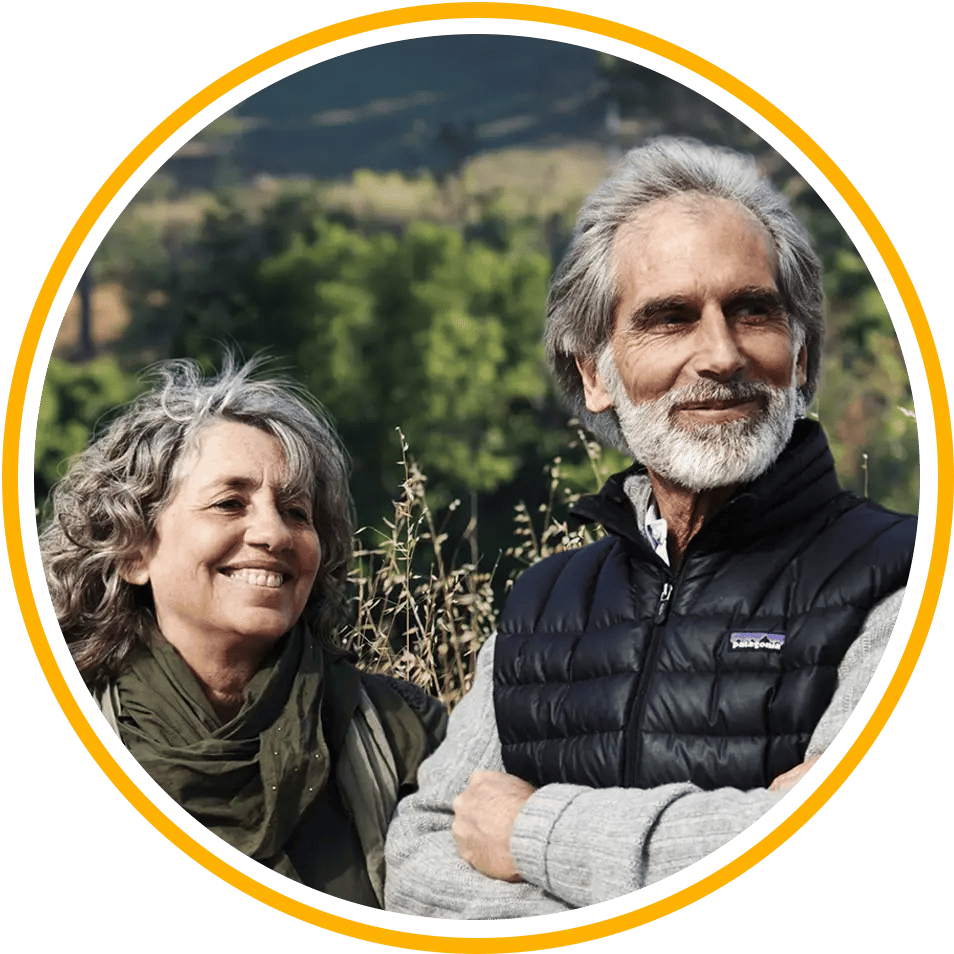
Drop us a line
If you'd like to learn more about how we can improve your operations, get in touch! We love a good challenge and we're ready to help.
.png?width=750&height=679&name=247Support%201(1).png)